The plans
The Site
We are proposing to locate our first UK facility at the Essar Stanlow Manufacturing Complex in Ellesmere Port, Cheshire. The site was chosen due to its industrial nature, a skilled local workforce and existing refinery infrastructure, including a direct pipeline access to pump and transport the SAF to UK airports through the Manchester Jet Line and the UK Oil Pipeline network (UKOP).
The site enjoys proximity to the green hydrogen by EET hydrogen (former Vertex), waste suppliers and to tie in connection points of other utility providers (National Gas, SPEN, United Utilities).
It also offers the opportunity to link into the HyNet North West carbon capture project. This could see process carbon emitted during the manufacture of SAF being captured and stored, reducing the overall net lifecycle carbon emissions of our fuel by up to 100% and thus creating a carbon neutral jet fuel. Fulcrum Bioenergy Ltd fuel is a ‘drop in’ renewable fuel with zero sulphur and very low levels of particulates, helping to improve local air quality, particularly around airports.
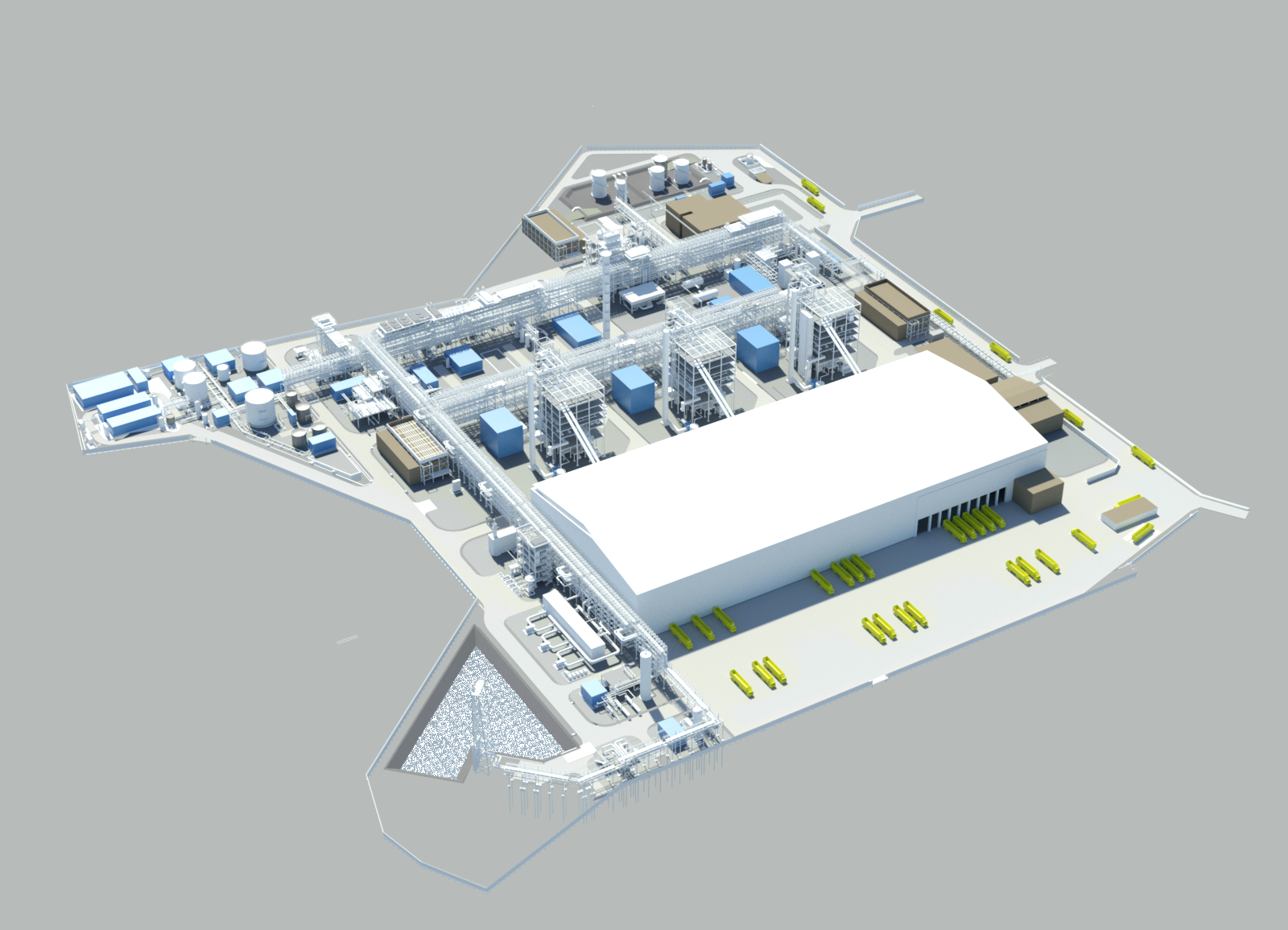
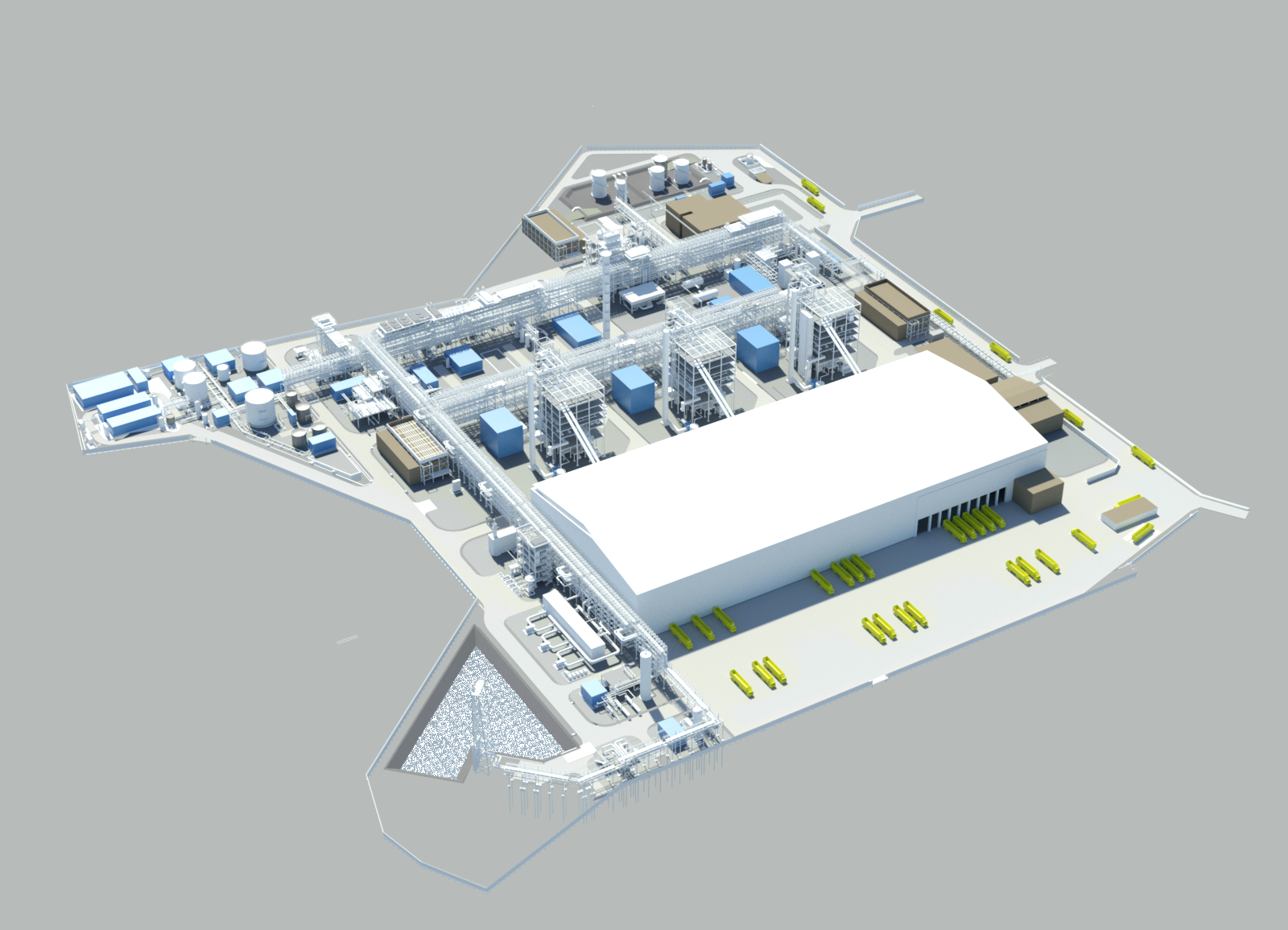
The technology
The Fulcrum propriety process uses a combination of proven technologies. Our integrated process has been proven in the United States, with the world’s first commercial scale SAF facility successfully producing low-carbon synthetic crude oil from waste at our Sierra BioFuels Plant in 2022.
Each year, the facility will receive 600,000 tonnes of pre-processed waste feedstock and convert it to approximately 100 million litres of SAF. This processed feedstock is mostly derived from Refuse Derived Fuel (RDF) which originates from household and commercial wastes.
Prior to being transported to the NorthPoint site, the feedstock is processed to remove further recyclables and other unsuitable materials, before a final light processing occurs on site to ensure the correct technical specification for SAF production.
Gasification technology is then used to create a synthesis gas (or ‘syngas’) from the processed feedstock which is then cleaned to remove any impurities. The cleaned syngas enters a process where liquid hydrocarbons are created which are then further upgraded into a low carbon, fully certified sustainable aviation fuel for use in aircraft.